|
Introduction
Since heat exchangers are highly customized in terms
of performance, software tools are needed in order to predict thermal characteristics, and
to size and design a
heat exchanger for a particular application.
Thermal prediction programs rely on two major components:
Firstly, an algorithm to simulate heat transfer from one medium to another. The central part is to describe the thermal resistance of an inner fluid, the separating wall and the outer fluid.
It requires input information (fluid type, inlet temperature, system pressure, flow rate, ambient temperature, altitude and approach velocity of the air) as well as other system constraints such as spatial limitations, power restrictions, etc.
The second component encompasses the mathematical description of the surface characteristics of compact heat exchanger cores. Since the design and technology of heat exchanger
cores are unique to each manufacturer, there
are no textbook solutions.
The analysis of the core consists of two steps: the actual
physical arrangement of inner and outer tubes and fins as well as material information, and dimensionless factors
that characterize the heat transfer (Colburne factors) and pressure drop (Fanning friction factors), on both sides of the heat exchanger. Theoretical analysis of the dimensionless factors alone proved to be not reliable. The solution to this problem is a Wind Tunnel Testing Facility that can be utilized for practical testing and data reduction using established procedures such as the Wilson plot and Steady-State methods.
Wind Tunnel Testing Facility
Global Heat Transfer recognizes the importance of Research and Development and its
increasing role in the industry and has developed
an in-house Wind Tunnel Testing Facility. The wind tunnel is used to collect data to
determine the performance characteristics of various coolers and core types.
Global Heat Transfer can also provide WIND TUNNEL TESTING CONSULTATION SERVICES. |
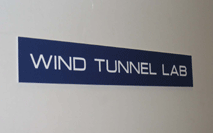 |
A wind tunnel is comprised of a converging and diverging tunnel sections, a test platform and a large fan. |
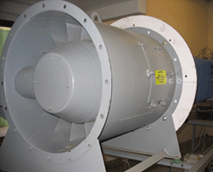 |
The fan provides a steady stream of air through the test section in order to determine the effects of airflow on the core test section, which remains fixed to the platform.
|
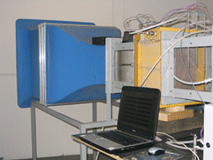 |
The wind tunnel is fitted with various sensors and transducers that are located
upstream and downstream of the cooler core. One of the measured properties is the temperature profile of the airflow before and after the core. A computer based
data acquisition system is used to collect the results.
The test section is approximately 13” x 13”.
|
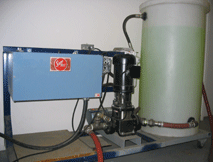 |
A heating unit and fluid reservoir regulate the flow rate and temperature of the control fluid
that is pumped through the core. |
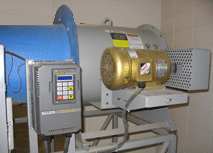 |
Once the data is collected, the information is evaluated using a thermal prediction
program
developed by Global Heat Transfer. The software utilizes heat transfer mechanics
to determine the various performance characteristics of the core types. |
|